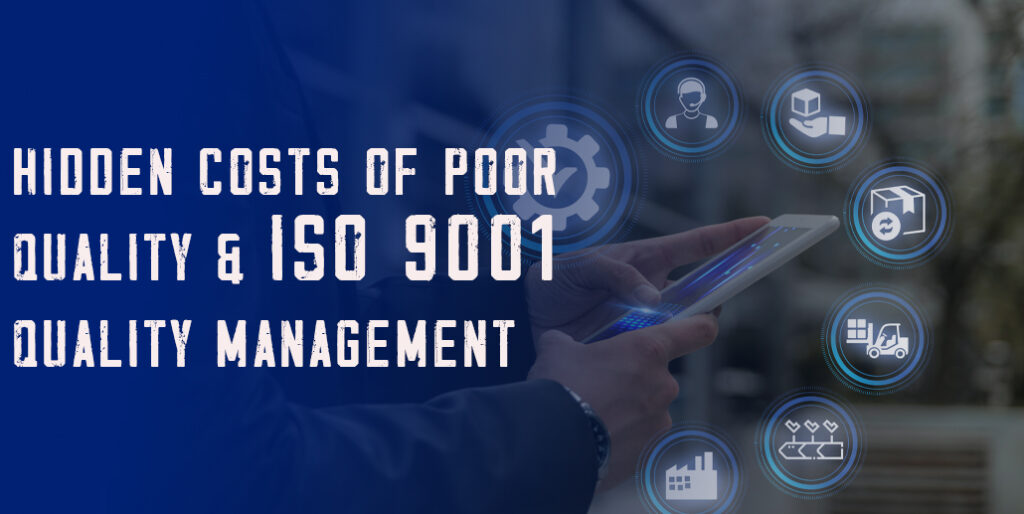
Poor quality may be one of the costliest mistakes a business can make, often without knowing its full impact. From remodel and product returns to consumer dissatisfaction and reputational damage, the hidden costs of mediocre quality can erode income and avoid growth. Many companies struggle with quality control, which leads to wasted resources and lost opportunities. ISO 9001 quality management gives an established framework to save you those costly problems. By enforcing its principles, companies can enhance efficiency, boost consumer satisfaction, and decrease monetary risks. This blog explores the financial and reputational expense of poor quality and the way ISO 9001 quality control serves as the primary solution.
The Financial Costs of Poor Quality
Businesses usually underestimate how much poor quality costs them. These hidden expenses are caused due to multiple reasons such as: remodel and scrap. Manufacturing defects, service errors, or wrong documentation usually requires companies to redo work, taking extra time, materials, and labour. This rework drives up operational expenses and decreases efficiency. For instance, a software development organisation that often releases buggy updates will spend substantial time solving problems rather than progressing with new features. Similarly, a factory generating faulty components may also have to scrap materials and reprocess orders, which can lead to losses.
Secondly, another cost that a business can incur is returns and assurance claims. When customers attain substandard products, they generally return them, therefore incurring refunds or replacements. Handling returns consists of logistics, inspection, and restocking charges. Additionally, businesses that offer warranties go through the cost of maintenance and replacements, which decreases the profit. For example, an electronics company with common defects may face many guaranteed claims, growing operational charges and damaging customer trust.
Thirdly, decrease in productivity and inefficiency. A poor-quality process results in delays and inefficiencies during many business functions. Employees spend time to repair issues instead of focusing on innovation or customer service. Poor documentation and lack of standardization additionally contribute to miscommunication and wasted effort. Consider a logistics organization that frequently misplaces orders due to inefficient tracking. These delays will frustrate the customers, lose their trust and disrupt operations. This will ultimately result in financial losses.
Lastly, penalties and legal liabilities that might occur. Non-compliance with organization requirements because of lack of quality can result in hefty penalties, lawsuits, and product recalls. Strict quality and safety regulations are enforced by regulatory agencies, and companies that violate them risk dire repercussions. A pharmaceutical business that produces defective drugs, for example, may be subject to legal action. Moreover, there may fines from the government, and even forced closures. Hence this can negatively affect the company’s revenues and reputation.
The Reputational Costs of Poor Quality
Beyond monetary losses, poor quality can harm a company`s reputation and a name in the market. This often leads to long term disadvantages for the business. A few risks are consumer dissatisfaction and poor evaluations. Customers assume constant quality with every purchase. When corporations fail to fulfill expectations, they face bad reviews, lawsuits, and a declining consumer base. In the digital era, with the increase in social media, online reviews have increased. when a customer is unsatisfied, the person takes no time to go online and give a bad review. a single bad review and feedback can decrease customer trust. Hence, damaging the company’s reputation. For example, an e-commerce store with frequent transport problems and faulty merchandise may also get negative reviews and feedback from customers. Which as a result, discourages other potential customers to buy your product or service.
Acquiring new customers is extra costly than keeping and retaining current ones. Poor quality results in increase in costs as dissatisfied consumer often switch to competitors. A business that have a reputation in the market for providing unreliable service will struggles to gain customer trust again. Consider a hotel chain that often gets lawsuits for unclean rooms or terrible customer service. Even discounts and promotions would not make amends for the poor perception of customers. Hence, this negatively affects brand credibility. A strong brand is known by consistent quality. Businesses that develop a reputation for terrible quality will not be able to attract investors or extend into new markets. For instance, a construction business that supplies subpar projects might struggle to win contracts from high-profile customers because they have a reputation of being unreliable.
How ISO 9001 Quality Management Reduces These Costs
ISO 9001 quality control is a globally identified standard that facilitates corporations to set up sturdy processes to prevent quality failures. By adopting ISO 9001 quality management, organizations can systematically decrease financial and reputational risks by following measures:
- Preventive Approach to Quality Issues: ISO 9001 quality control emphasizes proactive quality control instead of reactive fixes. Businesses should set up preventive measures for instance, threat assessments, internal audits, and quality checkpoints to discover potential problems beforehand. For example, a production business using ISO 9001 may also enforce real-time inspections, extensively decreasing defect costs and minimizing expensive rework.
- Standardized Processes for Efficiency: By documenting and standardizing strategies, ISO 9001 guarantees consistency in quality throughout different business operations. Employees comply with structured workflows, decreasing errors and inefficiencies. For instance, a healthcare provider that implements ISO 9001 can make sure constant patient care by adhering to clear protocols, decreasing misdiagnoses and procedural errors.
- Improved Customer Satisfaction: ISO 9001 requires businesses to prioritize consumer needs by collecting feedback, studying reviews, and constantly enhancing products and services. This attention on consumer satisfaction strengthens brand loyalty and minimizes poor experiences. For example, a software business which has ISO 9001 certification can systematically deal with consumer complaints and enhance software reliability, improving consumer trust.
- Reduced Costs Through Waste Reduction: ISO 9001 assists corporations to get rid of useless waste, optimize resource utilization, and decrease manufacturing costs. For instance, an automobile organization imposing ISO 9001 can streamline its supply chain. Hence, lowering material waste and decreasing manufacturing expenses.
- Compliance with Industry Standards: Many industries require strict adherence to quality standards. ISO 9001 certification demonstrates compliance, decreasing the risk of regulatory penalties, legal disputes, and decrease in business opportunities. For example, a food processing corporation with ISO 9001 certification is much more likely to secure contracts with huge retailers that demand high-quality assurance.
Conclusion
The hidden costs of bad quality such as monetary losses, inefficiencies, and reputational damage can significantly affect a business. Product returns, consumer dissatisfaction, and legal liabilities all contribute to unnecessary costs and prevent long-term growth. ISO 9001 quality management presents a structured method to removing those costs by enforcing preventive quality measures, standardizing processes, and improving consumer satisfaction. Businesses that get ISO 9001 certification helps to save cost and construct more strong brand credibility, making sure sustainable success.
If your business also struggles with quality issues, you should get ISO 9001 certification. Investing in quality management today will protect the business from negative image and reputation. Hence, securing your company’s future. For getting ISO 9001 certification, visit our website.